10 Ways to Boost the ROI of Your PdM Program
- Andrew Lewis
- Dec 22, 2022
- 5 min read
Updated: Feb 9, 2023
High ROI doesn't come easy... Focus on these key opportunities to achieve it.
Done well, an Industry 4.0 Predictive Maintenance (PdM) program will transform the performance of your industrial operation. We outline 10 waysto below. But these do not come easy. Achieving transformational results requires precise, intentional decisions. In our next blog post we outline 14 risk factors that will work against these opportunities.
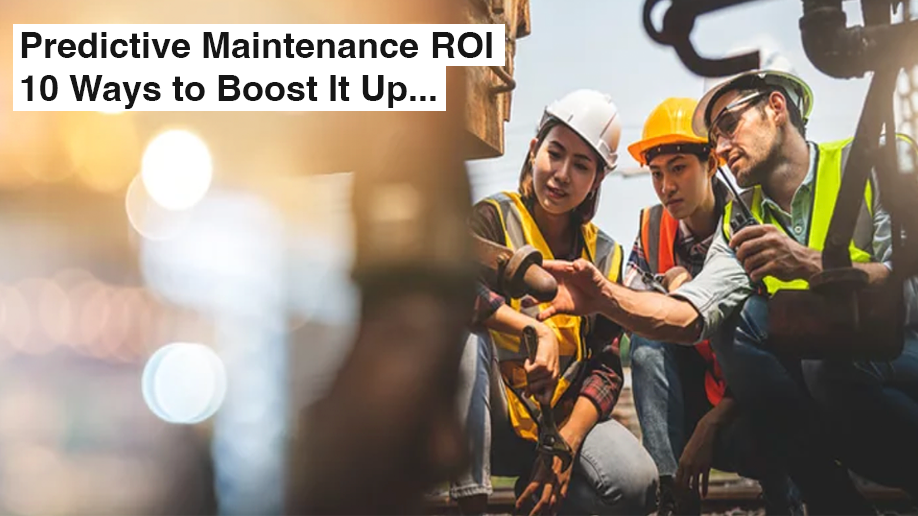
WHY IT MATTERS: We have demonstrated that a well planned and executed PdM program can produce ROIs as high as 60x across 234 assets. But this takes careful planning an execution of the opportunities outlined below.
BACKGROUND: Return on Investment (ROI) is calculated by dividing the profit earned on an investment (or cost) by the cost of that investment. This is the key KPI to determine the effectiveness of your POC and deployments, for a single asset or a group.
ROI = Profit/Cost
THE DETAILS: Your target ROI should be at least 10x to make the project worthwhile. As your PdM skills grow you can easily double that. Here are 10 opportunities to focus on. Most of these opportunities are for different use cases.
Boost Profits, Increase ROI:
Reduce Unplanned Downtime (UPDT) – This is the most common goal of a PdM program. UPDT hours are one of the costliest factors in an industrial operation, especially when it causes losses in production output. PdM sensors and AI algorithms can detect when a machine is starting to show signs of breakdown long before a maintenance technician can identify it. This advance detection enables technicians to proactively repair the equipment during a scheduled downtime, saving costly UPDT hours. Look for assets that are the leading cause of costly unplanned downtime that also match sensor types supported by your PdM platform.
Scale Technicians to Solve More Problems – A PdM program frees maintenance technicians from the repetitive tasks of walk arounds and the calculation of alarms. A PdM program will automatically generate these alarms for the technician. This typically expands the scope of asset coverage by a single technician by more than 10x. Look for failure diagnostics in selected assets for monitoring that match skill set of your organization.
Digitizing Legacy Assets – Many assets are not connected to a centralized monitoring system. On/off and failing conditions cannot be immediately determined. Rather than requiring a human inspection of the asset as a PM check, A PdM sensor can be used to establish a digital connection and provide real-time control room monitoring of the of the asset. Look for unmonitored assets that create lots of walk arounds for technicians or whose off-baseline status is slow to detect.
Quality Control – Assets that begin to fail will often fall out of calibration. This can degrade quality that is measured later in downstream inspections. PdM sensors can alert technicians of behavior that will contribute to loss of calibration before quality is affected. Look for assets whose degrdation or failure will impact quality.
Logistics Spare Parts Reduction – Reduce spare parts inventory with a shift toward just-in-time delivery of replacement parts. This eliminates the need to have a large inventory of spare parts on hand. Advance notice of unplanned repairs provides additional lead time for ordering parts, a valuable capability in today’s unpredictable supply chain. Look for assets that have long-lead or unpredictable ordering time.
Reduce Costs, Increase ROI:
Reduce Unplanned Maintenance Activities – A PdM program will allow maintenance to be more productive by scheduling activity proactively when it is most convenient (typically during a planned outage) rather than having to perform it on a reactive emergency basis. Look for assets that have failure modes that can be tracked with sensors selected.
Reduce Preventative Maintenance (PM) Activities – The second-stage goal of a PdM program after UPDT reduction has taken place. A PM program is a cornerstone of a traditional reliability-based maintenance program. There is significant labor attached to PMs. They are used as much for insurance value as to increase the asset's service life. The problem with PMs is they start with generic vendor service recommendations. Theses are not always effective because they do not account for unique operational loading of the asset. Then, PMs get added in reaction to an UPDT event, far exceeding the Corrective Maintenance (CM) work orders. Over the years, asset maintenance will accumulate layers of PMs. PM reduction is a second-stage cost reduction because it requires technician availability to remove these layers: eliminate redundancies and solve the underlying root cause of the failures. Look for assets that never fail and have a PM/CM work order ratio greater than six. This high ratio is usually attached to assets that have the highest cost of failure and overloaded with PMs to prevent them.
Enhance Worker Safety – Anticipate and prevent potentially dangerous or catastrophic scenarios before they occur, reducing the risk of injury and property damage. Repairs can be scheduled during a planned outage, reducing risk for technicians. Operator errors or off–book operation can be identified and corrected through training. Look for safety accidents and compliance failures and isolate those that can be caused by asset condition.
Reduce Compliance Violations – Some equipment failures or operator errors can cause safety violations, the release of toxic chemicals into the water and air that violate environmental standards. EPA and OSHA reporting is required, usually accompanied by fines. Look for compliance failures tied to asset operation or failures.
Employee Retention – Planned proactive repairs and PM reductions are the favorite jobs of technicians. Once they realize that an AI system will transform their job, they quickly overcome their fear of an AI system taking their jobs. They realize they will soon be in one of their favorite jobs: root cause analysis that engineers out the repair altogether. Look for skilled technicians and engage them in asset selection for ulimate PM reduction. They will become your greatest champions!
THE BOTTOM LINE: AI-based predictive maintenance is already having a significant impact on plant operations. To remain competitive in today's market place requires all industrial operations, big and small, to start the journey to predictive maintenance.
PRIOR POST: Scaling Your Predictive Maintenance Program
GetIQ.ai is a blog about building AI solutions for augmenting decision making and empowering people that make them. It's authored by the engineers at DecisionIQ.
ABOUT DECISIONIQ: We are "boots on the ground" factory engineers expert at the adoption of AI and machine learning into operations. As consultants and system integrators we bring our experience in a mix of a well structured programs that enable our clients to produce winning results and maximum ROI. You will learn to use AI to build competitive advantage by increasing plant uptime, quality and yield. With 24 POCs and 16 deployments we have achieved for our client’s ROIs as high as 60x and a cumulative $22 million in savings.
AN AWS PARTNER: We provide capability in design of AI solutions for industrial applications. We work with the AWS Industrial IoT services stack, cloud migrations and Amazon Monitron POCs and deployments. For qualifying customers, many of these capabilities are eligible for AWS subsidized funding.
©Copyright 2023, DecisionIQ, Inc.
Comments